TANIOBIS optimizes niobium alloys for challenging operating conditions
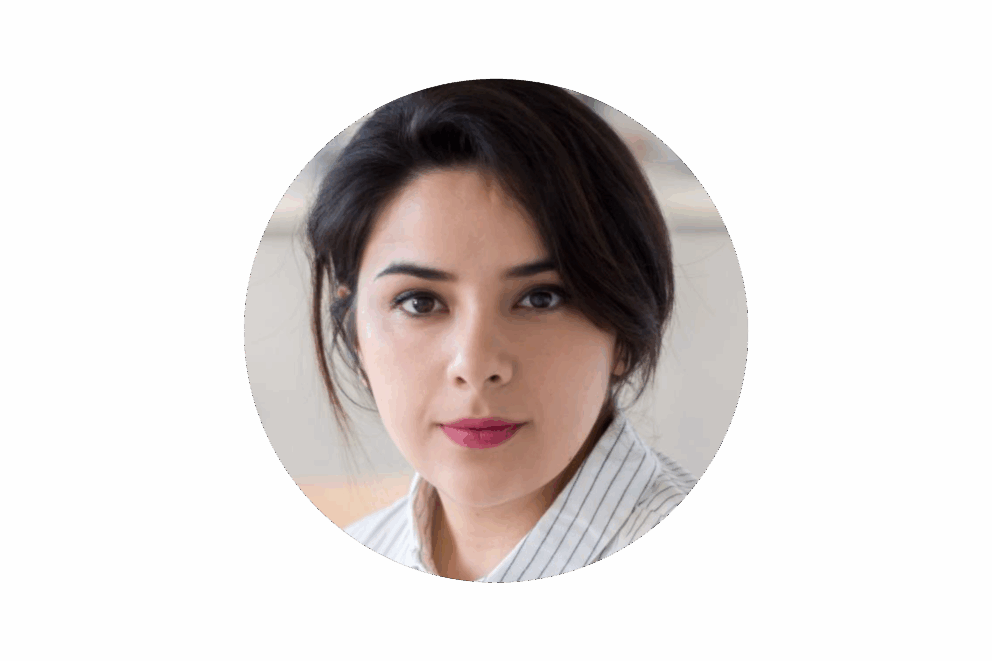
Focusing on high-temperature materials: An interview with Dr. Bahar Fayyazi
Dr. Bahar Fayyazi, the Product Manager for Metal Powder and Additive Manufacturing at TANIOBIS, talks about the development of niobium alloys, their use in additive manufacturing and the importance of these materials in the aerospace industry. The company is currently setting new standards for using these innovative, high-temperature materials in the most challenging environments.
What brought you to TANIOBIS and what is your current role there? What motivates you in your work?
Bahar Fayyazi: After completing my PhD in materials science, I wanted to build a career at a company that is actively engaged in the research and development of high-performance materials and their use in innovative technologies. My particular interest in powder metallurgy and additive manufacturing perfectly matched the current activities at TANIOBIS. However, I was also looking for a position that involves management responsibility. I was therefore able to take on the role of product manager for powders in the field of additive manufacturing and related processes.
I was particularly enthusiastic about becoming part of an experienced, committed and interdisciplinary team and working in a research-intensive environment that explicitly encourages fresh ideas. I was also fascinated by the prospect of using our materials to help develop future-oriented technologies in dynamic sectors like aerospace and medical engineering.
What are the unique selling points that set TANIOBIS apart from its competitors?
Bahar Fayyazi: TANIOBIS has had decades of experience in processing materials based on niobium and tantalum – and it has unrivaled expertise in the field of particle design on all length scales. TANIOBIS also offers customized solutions for a wide range of industries, and an experienced application technology team is available to support its research and development unit. Our company also controls the entire supply chain, so ensuring reliable raw material procurement, sustainable production and the consistent availability of products.
In the field of additive manufacturing, we are the leading producers of customized alloy powders based on refractory metals, which are then adapted to meet specific requirements. Our portfolio goes far beyond just conventional niobium alloys: We are developing high-performance materials that are setting new standards in additive manufacturing.
Conventional niobium alloys were already in use in the 1970s. How did TANIOBIS remodel these alloys so that they are suitable for 3D printing?
Bahar Fayyazi: That is right, several niobium alloys were developed back in the 1960s and 1970s; NASA was the particular driving force behind research in this field. Probably the best known of these is C-103, an alloy based on niobium, hafnium and titanium. Due to its comparatively good processing and welding properties – other niobium alloys were very difficult to process conventionally – it is still being sold commercially with great success.
These materials are currently experiencing a renaissance thanks to the ongoing development of additive manufacturing, which enables the comparatively cost-effective direct production of components with complex structures from digital models. TANIOBIS recognized this early on and seized the opportunity of further developing these alloys for use in additive manufacturing. We have identified even higher-performance niobium alloys with improved high-temperature properties and developed pre-alloyed powders that are particularly suitable for 3D printing. We can therefore offer optimized solutions to meet changing requirements, especially in the aerospace industry.
In which fields of application do you see the greatest demand, especially in the aerospace industry?
Bahar Fayyazi: Niobium alloys are widely used in space propulsion systems, particularly in reaction control and attitude control thrusters, which are vital for precisely maneuvering satellites and spacecraft during space exploration missions. These alloys are used in jet engine components, rocket nozzles, and other structural parts that are subject to extreme heat and mechanical stress in the space sector. Niobium alloys are also ideal for meeting the rigorous demands of defense technologies, like hypersonic vehicles and advanced missile systems.
What particular advantages do these alloys offer in such high-temperature fields?
Bahar Fayyazi: Niobium and its alloys have exceptional properties that make them perfect for high-temperature environments. With a melting point of over 2,000°C, they are ideally suitable for extreme thermal loads.
When compared to nickel-based superalloys, which are currently being used in high-temperature applications, niobium alloys have a similar density, but offer significantly higher temperature resistance. While nickel-based alloys can withstand a maximum temperature of about 1,100°C, certain niobium alloys remain mechanically stable at operating temperatures exceeding 1,700 °C. Niobium alloys also exhibit low thermal expansion, so that no deformation occurs, even in extreme thermal conditions.
What specific properties of the alloys would you like to highlight and how do they affect performance in extreme conditions?
Bahar Fayyazi: The niobium alloys provide several key advantages in extreme conditions. Their outstanding high-temperature stability ensures structural integrity in the most demanding thermal conditions. They also have exceptional creep resistance, which means they can resist material deformation caused by the passing of time or high temperatures when exposed to mechanical stress. This property considerably extends the service life of components in this environment. Finally, their excellent thermal conductivity allows efficient heat dissipation, which effectively prevents any overheating and maintains optimal performance.
How do you view the market potential for these alloys?
Bahar Fayyazi: The market potential for alloys is significant, especially in high-performance industries like aerospace, aviation and defense. These industries are increasingly requesting materials that can withstand extreme conditions, are durable and offer improved performance. Our alloys precisely meet these requirements. The growing use of additive manufacturing is further unlocking new possibilities for customized applications. This is enhancing the versatility and adaptability of our alloys and is opening up new market opportunities.
To what extent can TANIOBIS appraise and adapt the composition of its alloys to meet customer requirements?
Bahar Fayyazi: TANIOBIS specializes in producing high-entropy alloys (HEAs) based on refractory metals and is collaborating closely with several customers, primarily research institutes and universities, to develop these advanced materials. We have already produced numerous HEAs, which, in extreme cases, may consist of more than ten different elements.
Does this pose any challenges and, if so, what are they?
Bahar Fayyazi: One of the greatest challenges involves having a homogenous alloying process for all the constituent elements when they have very different melting points. To cope with this, we are focusing on optimizing production techniques and refining the alloying process to ensure that these complex compositions meet the high standards required for their intended applications. Individually adapting alloy compositions to customer requirements requires both technical expertise and a deep understanding of how materials behave at high temperatures and in different processing conditions.