TANIOBIS optimiert Nioblegierungen für anspruchsvolle Einsatzbedingungen
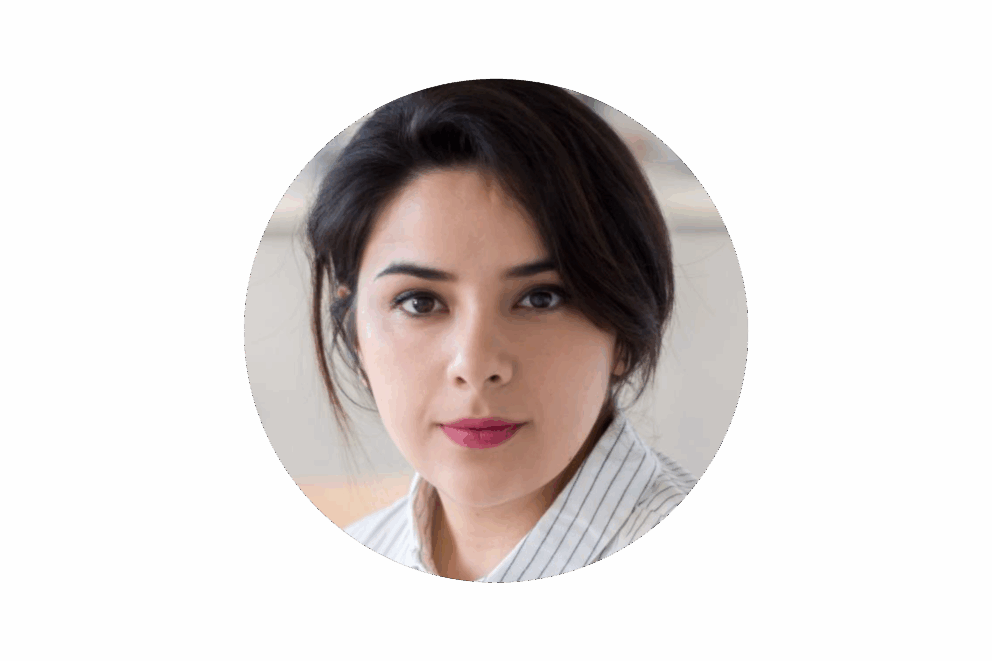
Hochtemperaturwerkstoffe im Fokus: Interview mit Dr. Bahar Fayyazi
Dr. Bahar Fayyazi, Produktmanagerin für Metallpulver und additive Fertigung bei TANIOBIS, spricht im Interview über die Weiterentwicklung von Nioblegierungen, deren Einsatz in der additiven Fertigung und die Bedeutung dieser Werkstoffe für die Luft- und Raumfahrt. Das Unternehmen setzt mit diesen innovativen Hochtemperaturwerkstoffen aktuell neue Maßstäbe für anspruchsvollste Anwendungen.
Was hat Sie zu TANIOBIS geführt und welche Rolle haben Sie dort aktuell? Was motiviert Sie an Ihrer Arbeit?
Bahar Fayyazi: Nach meiner Promotion im Bereich Materialwissenschaften strebte ich eine berufliche Laufbahn in einem Unternehmen an, das sich aktiv mit der Erforschung und Entwicklung von Hochleistungsmaterialien und deren Anwendung in innovativen Technologien befasst. Mein besonderes Interesse an der Pulvermetallurgie und der additiven Fertigung passte perfekt zu den aktuellen Aktivitäten bei TANIOBIS. Gleichzeitig suchte ich eine Position mit Managementverantwortung. So ergab sich für mich die Chance, als Produktmanagerin für Pulver im Bereich der additiven Fertigung und verwandter Verfahren Verantwortung zu übernehmen.
Mich begeisterte besonders, Teil eines erfahrenen, engagierten und interdisziplinären Teams zu werden und in einem forschungsintensiven Umfeld zu arbeiten, in dem neue Ideen ausdrücklich gefördert werden. Zudem faszinierte mich die Perspektive, mit unseren Materialien zur Entwicklung zukunftsweisender Technologien in dynamischen Branchen wie der Luft- und Raumfahrt sowie der Medizintechnik beizutragen.
Mit welchen Alleinstellungsmerkmalen hebt sich TANIOBIS von der Konkurrenz ab?
Bahar Fayyazi: TANIOBIS verfügt über jahrzehntelange Erfahrung in der Verarbeitung von Materialien auf Basis von Niob und Tantal sowie eine unübertroffene Expertise im Bereich des Partikeldesigns auf allen Längenskalen. Darüber hinaus bietet TANIOBIS maßgeschneiderte Lösungen für unterschiedlichste Branchen, wobei das Team aus der Forschung und Entwicklung von einer qualifizierten Anwendungstechnik unterstützt wird. Zudem kontrollieren wir die gesamte Lieferkette, was eine zuverlässige Rohstoffbeschaffung, eine nachhaltige Produktion und eine gleichbleibende Produktverfügbarkeit sicherstellt.
Im Bereich der additiven Fertigung sind wir führend in der Herstellung individuell nach Kundenwunsch gefertigter Legierungspulver auf Basis von Refraktärmetallen, die auf spezifische Anforderungen zugeschnitten sind. Unser Portfolio geht weit über konventionelle Nioblegierungen hinaus: Wir entwickeln Hochleistungswerkstoffe, die durch additive Fertigung neue Maßstäbe setzen.
Konventionelle Nioblegierungen wurden bereits in den 1970er Jahren verwendet. Wie hat TANIOBIS diese Legierungen neu konzeptioniert und sie für den 3D-Druck zugänglich gemacht?
Bahar Fayyazi: Das stimmt, mehrere Nioblegierungen wurden bereits in den 1960er- und 1970er-Jahren entwickelt, wobei die Erforschung insbesondere von der NASA vorangetrieben wurde. Die wohl bekannteste darunter ist C-103, eine Legierung auf Basis von Niob, Hafnium und Titan. Aufgrund ihrer vergleichsweise guten Verarbeitbarkeit und Schweißbarkeit – andere Nioblegierungen ließen sich nur sehr schwer konventionell verarbeiten – wurde und wird diese noch immer kommerziell erfolgreich vertrieben.
Mit der Weiterentwicklung der additiven Fertigung, die eine vergleichsweise kostengünstige Darstellung von Bauteilen mit komplexen Strukturen direkt aus digitalen Modellen ermöglicht, erleben die Materialien gerade eine Renaissance. TANIOBIS hat dies früh erkannt und die Chance ergriffen, die Legierungen mit einem Fokus auf die Anwendung in der additiven Fertigung weiterzuentwickeln. Wir identifizierten dabei noch leistungsfähigere Nioblegierungen mit verbesserten Hochtemperatureigenschaften und entwickelten speziell für den 3D-Druck maßgeschneiderte, vorlegierte Pulver. Wir bieten somit optimierte Lösungen für die sich wandelnden Anforderungen vor allem in der Luft- und Raumfahrtindustrie.
In welchen Anwendungsbereichen, insbesondere in der Luft- und Raumfahrt, sehen Sie die größte Nachfrage?
Bahar Fayyazi: Derzeit besteht Nachfrage nach Nioblegierungen vor allem für den Einsatz in Triebwerkskomponenten, die zur Reaktionskontrolle und Lageregelung und somit für ein präzises Manövrieren von Satelliten und Raumfahrzeugen im Orbit notwendig sind. In der Raumfahrt finden sie Verwendung in Triebwerkskomponenten, Antriebsdüsen und weiteren strukturellen Bauteilen, die hohen Temperaturen und mechanischen Belastungen ausgesetzt sind. Auch in Verteidigungstechnologien wie etwa in Hyperschallflugkörpern und neuartigen Raketensystemen spielen Nioblegierungen eine zentrale Rolle.
Welche besonderen Vorteile bieten diese Legierungen bei solchen Hochtemperaturanwendungen?
Bahar Fayyazi: Niob und seine Legierungen zeichnen sich durch außergewöhnliche Eigenschaften aus, die sie ideal für Hochtemperaturumgebungen machen. Mit einem Schmelzpunkt von über 2.000 °C sind sie bestens für extreme thermische Belastungen geeignet.
Im Vergleich zu Superlegierungen auf Nickelbasis, die gegenwärtig in Hochtemperaturanwendungen eingesetzt werden, haben Nioblegierungen eine ähnliche Dichte, bieten aber eine deutlich höhere Temperaturbeständigkeit. Während Nickel-Basislegierungen maximal 1.100 °C standhalten, bleiben bestimmte Nioblegierungen bei Betriebstemperaturen von über 1.700 °C mechanisch stabil. Darüber hinaus weisen Nioblegierungen eine geringe Wärmeausdehnung auf, sodass selbst unter extremen thermischen Bedingungen keine Verformung auftritt.
Welche spezifischen Eigenschaften der Legierungen möchten Sie hervorheben und wie wirken sie sich auf die Leistung unter extremen Bedingungen aus?
Bahar Fayyazi: Unsere Nioblegierungen spielen ihre Vorteile vor allem in extremen Umgebungen aus. Beispielsweise gewährleistet ihre herausragende Hochtemperaturstabilität strukturelle Integrität unter anspruchsvollsten thermischen Bedingungen. Hier sind sie den gegenwärtig eingesetzten Superlegierungen auf Nickelbasis deutlich überlegen. Zudem verfügen sie über eine außergewöhnliche Kriechbeständigkeit, also die zeit- und temperaturabhängige Verformung eines Werkstoffes unter Last. Diese Eigenschaft verlängert die Lebensdauer von Bauteilen unter hoher Belastung erheblich. Schließlich sorgt ihre hohe Wärmeleitfähigkeit für eine effiziente Wärmeableitung in kältere Bauteilbereiche, wodurch eine lokale Überhitzung vermieden wird und die Leistungsfähigkeit des Gesamtbauteils erhalten bleibt.
Wie schätzen Sie das Potenzial dieser Legierungen auf dem Markt ein?
Bahar Fayyazi: Das Marktpotenzial der Legierungen ist erheblich, insbesondere in Hochleistungsindustrien wie Raumfahrt, Luftfahrt und Verteidigung, da diese Industrien zunehmend Materialien benötigen, die extremen Bedingungen standhalten, langlebig sind und eine verbesserte Performance aufweisen. Unsere Legierungen erfüllen genau die dafür notwendigen Anforderungen. Zudem eröffnet der wachsende Einsatz der additiven Fertigung zusätzliche Möglichkeiten für maßgeschneiderte Anwendungen. Dies steigert die Vielseitigkeit und Anpassungsfähigkeit unserer Legierungen und eröffnet neue Marktchancen.
Inwieweit ermöglicht TANIOBIS die Anpassung und Bewertung der Legierungszusammensetzung entsprechend den Kundenanforderungen?
Bahar Fayyazi: TANIOBIS ist auf hochentropische Legierungen (HEAs) auf Basis von hitzebeständigen und besonders korrosionsbeständigen Refraktärmetallen spezialisiert und arbeitet eng mit Forschungseinrichtungen und Universitäten zusammen, um diese fortschrittlichen Materialien zu entwickeln. Wir produzierten bereits zahlreiche HEAs, die im Extremfall aus mehr als zehn verschiedenen Elementen bestehen können.
Ergeben sich dabei Herausforderungen und wenn ja welche?
Bahar Fayyazi: Eine der größten Herausforderungen ist die homogene Legierungsbildung, da die enthaltenen Elemente stark unterschiedliche Schmelzpunkte aufweisen können. Aus diesem Grund optimieren wir kontinuierlich unsere Produktionsverfahren, insbesondere durch die Verfeinerung der Legierungsprozesse. Dies stellt sicher, dass die Legierungen die hohen, für die spezifischen Einsatzbereiche notwendigen Anforderungen erfüllen. Die individuelle Anpassung der Legierungszusammensetzungen an die Kundenwünsche erfordert sowohl ein tiefgehendes Materialwissen als auch ein ebensolches Prozessverständnis.